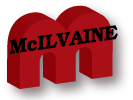
Coronavirus
Technology Solutions
April 24, 2020
Safe and Cost Effective Food Processing in the
COVID-19 Era
APC Filtration has New Mask Media
Cummins will Make Respirator Filters At One of
its Diesel Filter Plants
AquiSense Launches UV-C LED Surface Disinfection
System
Axalta Powder Coatings Kill Viruses in Thirty
Minutes
Use the Air Vent Above Each Airline Passenger
and Plastic Curtains to Provide Laminar Downward
HEPA Filter Air Flow
ExxonMobil has New Filtration Fabric and Mask
Design
ExxonMobil is Increasing Isopropyl Alcohol
Production and Also Producing Medical Grade
Sanitizer
Porvair Filtration Group’s Segensworth Division
to Supply Fully Assembled Face Shields to the
British National Health Service
_____________________________________________________________________________
Safe and Cost Effective Food Processing in the
COVID-19 Era
The food processing industry is facing a huge
problem with plants deemed essential
experiencing virus outbreaks. There is the
opportunity to take advantage of new products
and mitigation technologies and not only create
safe working conditions for employees but to
reduce risk of product contamination. An
additional benefit is to improve product
quality. Studies have shown that cleaner
environments can result in extension of pork
shelf life by 12 days. Here are some of the
mitigation technologies which can be employed.
Plant
Entrance
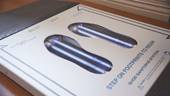
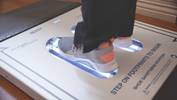
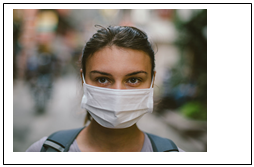
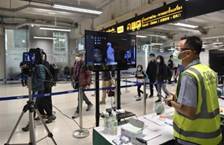
Plant
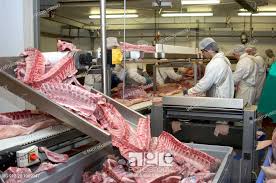
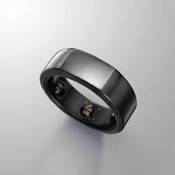
Offices, Lunch and Locker Rooms
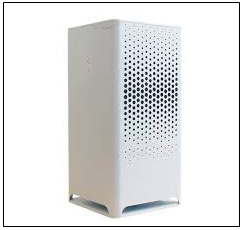
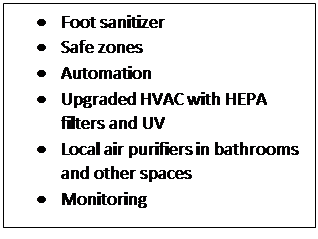
There are many new technologies which will
find widespread use.
It is now well established that virus
clouds are airborne and travel long distances.
Therefore efficient masks will be necessary.
Nanofiber membranes offer higher efficiency and
comfort in masks.
Robots can monitor conditions as they
move throughout the plant. Viruses have been
proven to be transmitted by shoe soles.
So there are now foot sanitizers. HEPA
filters can remove viruses in HVAC and local
room purifier systems.
APC Filtration has New Mask Media
Due to a call from the
federal government, APC Filtration understands
the timely importance of protecting our
communities by producing these vital materials
in Canada.
With over 35 years in the air
filter industry, APC Filtration is devoted to
increasing supplies, and investing in product
innovation to respond to these growing demands.
In collaboration with several research leaders
such as McMaster, Ryerson, Woodbridge Group and
private manufacturers, APC Filtration is
tackling this critical shortage by producing a
variety of face masks, and ventilator filters
that will help protect residential and
commercial spaces with quality air. Production
and manufacturing is 100% proudly Canadian.
In efforts with McMaster
Engineers helping frontline workers, APC has
provided in-house pressure drop and aerosol
rejection testing for L3 surgical and N95 masks.
In addition, APC has developed a new filter
media for mask production, which samples were to
be ready for ASTM testing on April 17th.
Cummins will Make
Respirator Filters At One of its Diesel Filter
Plants
Cummins will convert one of its diesel filter
plants to produce particulate filters used in
respirators for health care professionals in the
fight against COVID-19.
Cummins reached an agreement with 3M to
manufacture high efficiency particulate filters
for use in the latter’s powered air purifying
respirators (PAPRs).
Cummins will use existing manpower and equipment
at its Neillsville, Wisconsin facility to pleat
the media, assemble it into cartridge housings
and do final testing before shipping the filters
to Valley, Nebraska, where 3M’s PAPRs are
manufactured.
Production of the filters at Cummins’
Neillsville location is expected to begin by the
end of April.
“Cummins has been striving to find ways to help
during the COVID-19 crisis,” said Tom Linebarger,
Chairman and Chief Executive Officer of Cummins.
“Working with 3M, we discovered our technologies
and manufacturing expertise could be relevant as
we partner in new ways to help protect
healthcare professionals.”
PAPRs are used by front-line healthcare workers
responding to the COVID-19 pandemic. PAPRs use a
battery-powered blower that sends filtered air
into a hood or head top that covers the wearer’s
head or face; and can provide increased levels
of respiratory protection, especially for
critical healthcare situations such as aerosol
generating procedures.
The partnership has the potential to more than
double the current production of filters for
3M’s PAPRs. The additional filters are needed as
3M has ramped up production of PAPRs to meet a
surge in demand for personal protective
equipment due to the COVID-19 outbreak.
“3M continues to work around the clock to get
personal protective equipment, including PAPRs,
to the heroic healthcare workers and first
responders on the frontlines of the COVID-19
fight,” said Mike Roman, 3M Chairman of the
Board and CEO. “Our partnership with Cummins
will help us produce more of this critical
equipment in the coming months.”
Cummins’ filtration business line designs,
manufactures and sells air, fuel, hydraulic and
lube filtration, as well as chemical technology
products for diesel and gas-powered equipment
around the world.
AquiSense Launches UV-C LED Surface Disinfection
System
PearlSurface 24G9 is designed for health care
applications such as reuse of N95 face mask and
other PPE.
AquiSense Technologies, a US-based maker of
ultraviolet (UV) LED disinfection technology,
has launched the PearlSurface 24G9, one of the
first UV-C LED surface disinfection products
designed for health care applications such as
reuse of N95 face mask and other PPE.
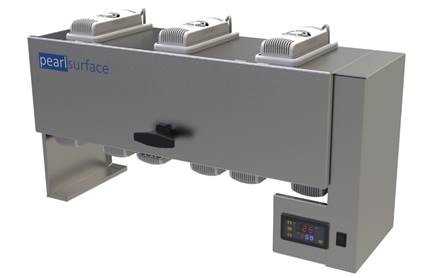
The PearlSurface 24G9 offers advanced benefits
specific to LEDs, including mercury-free lamps,
instant-on operation and low cost of ownership,
while providing high-power density, homogeneous
disinfection of target objects.
According to the company, the PearlSurface 24G9
offers simple operation, integrated timer, low
voltage power supply and compact footprint,
making it suitable for point-of-use hospital
settings, care homes, ambulances, police/fire
departments, factories, food preparation, etc.
AquiSense says it will offer this product under
the current US FDA enforcement relief to deal
with immediate COVDI19 emergency use and will
simultaneously submit a premarket approval
application.
“We accelerated our product development pipeline
in response to immediate global needs for
reliable reuse disinfection products,” said
Oliver Lawal, CEO at AquiSense Technologies. “We
are fortunate to be able to leverage an existing
high-output UV-C LED module from our water
treatment products and draw on our experience in
rapid hardware design and optical modeling to
ensure a high-level disinfection efficacy.”
concluded Lawal. AquiSense Technologies is
interested in talking to potential partners and
distributors for the PearlSurface 24G9.
Axalta Powder Coatings Kill Viruses in Thirty
Minutes
Axalta will supply E&R Powder Coating with more
than 7,000 pounds of its Alesta AM powder
coatings for bed frames at a temporary hospital
at McCormick Place in Chicago, IL, which is
being used for coronavirus patients.
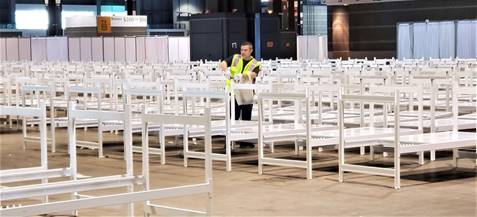
.
"Axalta's Alesta AM is being applied to these
new beds to ensure that the surfaces are
protected with silver zinc zeolite antimicrobial
technology that is known to inhibit the growth
of microbes on powder coated surfaces,"
said Michael Bollan, Americas Business Director
for Axalta Powder Coatings. "We are proud to be
a significant producer of antimicrobial powder
coatings and are actively exploring new
applications for this important part of Axalta's
product portfolio, including for potential use
in automotive interiors."
"Axalta cares about our communities around the
world," continued Bollan. "We appreciate being a
part of the solution to provide a high-quality
coated surface for hospital patients in this
time of critical need."
Alesta AM powder coatings provide protection
that is ideal for hospitals, public transit,
medical equipment, water treatment plants, food
service packaging equipment, pharmaceutical
labs,
Use the Air Vent Above Each Airline Passenger
and Plastic Curtains to Provide Laminar Downward
HEPA Filter Air Flow
The air vent above each passenger seat can be
the means by which HEPA filtered air flows
downward around the passenger and then is
exhausted at floor level thereby protecting the
passenger.
McIlvaine Company speculates that
short
retractable plastic curtains could separate
passengers.
Since each would have their own air flow
source this arrangement would be just as safe as
having just one passenger per row. The cost of
the curtains would be minuscule and the ability
to fly with a full load of passengers would be
very remunerative. Each seat could be viewed as
a personal shower area except it would be air
not water.
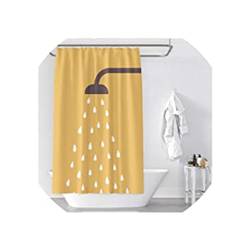
Some research uncovered the following insights.
Travel + Leisure spoke to Dr. Mark Gendreau —
the medical director and vice chair of emergency
medicine at Lahey Medical Center-Peabody, and an
expert on the spread of infectious diseases
associated with air travel — to learn how it
works and how travelers can best utilize the air
vents.
As a rule of thumb, the air that you’re
typically breathing and exposed to is usually
anywhere from two to five rows surrounding your
seat,” he added.
Here's how the ventilation systems work.
Each of these sections (known as temperature
control zones), receives air from overhead
distribution nozzles that flows through the
length of the cabin. The air exits the plane
through a grill that's often located beneath the
windows, or where the side walls meet the floor
of the plane.
This air then combines with the air outside
before going through a HEPA (High Efficiency
Particulate Air) to clear away dust and microbes
before re-entering the plane.
The number of these ventilation zones varies
depending on the aircraft, but each zone
typically goes through this filtration process
15 to 30 times within the hour, with 50 percent
of the air getting re-circulated and 50 percent
of the air coming from outside, according to
Gendreau.
The systems were primarily designed during the
time when smoking was permitted on flights,
Gendreau said, meaning airlines had to come up
with an efficient and regular filtration system
for their ventilation to clear the smoke from
the cabins.
For this reason, HEPA filters can remove more
than 99 percent of dust and microbes in the air,
Gendreau said, though there are times where
you'll want to turn to your personal vent.
“For
airborne viruses, it is incredibly important to
ventilate, since ventilation becomes your main
means of control besides isolating the affected
person,” Gendreau said.
Airborne viruses, like tuberculosis and measles,
are transmitted by tiny droplet nuclei that can
hang in the air for up to five hours, Gendreau
said.
While viruses associated with the common cold
and upper respiratory tract infections tend to
be larger in size and heavier (consequently
falling to the floor rather quickly), these
particles linger. Which is where your vent comes
in.
By using the vent and turning it on medium or
low, you can create an invisible air barrier
around you that creates turbulence —
simultaneously blocking these particles and
forcing them to the ground faster.
ExxonMobil has New
Filtration Fabric and Mask Design
In response to the unprecedented challenges from
the COVID-19 pandemic, ExxonMobil is applying
its deep knowledge and experience with
polymer-based technologies in combination with
GCMI to facilitate development and expedite
third-party production of innovative safety
equipment that can be sterilized and worn
multiple times.
A new industrial-style mask is being
fast-tracked for production. The design improves
coverage of a health care worker’s nose and
mouth and will use a replaceable cartridge
system that includes a filtration fabric to
prevent contact spread of the virus from the
saturated filter. In this design, the filters
are disposable while the main component of the
mask can withstand repeated sterilization, thus
prolonging the life-cycle of the product and
addressing shortages of N95 masks.
Prototypes are currently being tested and
reviewed by the U.S. Food and Drug
Administration. When approved, production will
begin immediately, with ExxonMobil supporting
the identification of manufacturers familiar
with the materials and process to quickly
deliver the masks to doctors, nurses and health
care providers. Once approved, manufacturers
indicate they will be able to produce as many as
40,000 ready-to-use masks and filter cartridges
per hour.
"Expediting advanced technologies to help those
who are combatting this global pandemic is
absolutely critical for society," said Karen
McKee, president of ExxonMobil Chemical Company.
"We’re proud to do our part by sharing our
expertise and experience in material
technologies, and energy supplies needed to
support our health care workers. It’s just one
example of ExxonMobil employees working around
the clock to help keep our communities safe and
limiting the spread of COVID-19."
"Scaling solutions rapidly to address the global
crisis requires significant investment,
innovation and collaboration," said Tiffany
Wilson, CEO of Global Center for Medical
Innovation. "By partnering with ExxonMobil,
we’re harnessing the expertise and capabilities
of the world’s largest energy companies to
accelerate our ability to realize that vision."
Another product developed by GCMI is a face
shield made from high-grade polymers that can
withstand the harsh conditions of sterilization
to enable reuse, while meeting the visibility
and safety requirements of current designs. The
technology complies with existing safety
standards, reducing the time from design to
front-line use. More than 50,000 units have
already been produced and are being distributed
to hospitals in New York and Atlanta. Production
facilities are ramping up to manufacture more
than 170,000 shields per hour in the coming
days.
GCMI verifies, validates and accelerates the
development and commercialization of new medical
technologies that save lives and improve patient
care. GCMI has worked collaboratively during
COVID-19 to design, develop, prototype, validate
and execute the need for protection to frontline
healthcare workers, with an efficient, quick
process intended to save lives.
ExxonMobil, which invented filtration fabric
technology in the 1960s, is making its experts
available to provide technical expertise and
delivering polypropylene from its manufacturing
sites in Baytown, Texas and Baton Rouge,
Louisiana. The raw materials will be expedited,
if needed, for face mask assembly. The company
will also facilitate supply chain interfaces to
expedite deployment.
The initiative is a collaboration between GCMI;
Dr. Joanna Newton, Pediatric
Hematologist/Oncologist, Aflac Center and Blood
Disorders Center of Children’s Healthcare of
Atlanta and Assistant Professor of Pediatrics,
Emory University School of Medicine; Children’s
Healthcare of Atlanta Pediatric Technology
Center; and a team of scientists and researchers
at the Georgia Institute of Technology and its
Invention Studio.
Justin Sink, a digital transformation and
innovation advisor at ExxonMobil, answered
questions about the masks.
The masks are made
of a material that Exxon invented in the 1970s.
It looks and feels like rigid cloth, but it’s
actually a melt-blown polymer that enables air
to flow in and out easily. What most people
don’t know is that before the fabric is shaped
into masks, it’s given an electrostatic charge.
That charge is what captures viruses or
bacteria.
Over time and with extended use and
contamination, that charge diminishes and, along
with it, the protective ability of the mask. So,
these masks often have to be thrown away after a
single use. And the problem is there’s only so
much of the fabric being produced around the
world.
With the N95 mask, the technology that’s
required to produce each unit is quite complex.
It’s difficult to build a new supply chain for
N95 masks in a week – it usually takes months.
And the virus spreads exponentially.
For context, says Sink “ we still produce the
raw materials for the fabric at our Baytown,
Texas, production facility, which is currently
working at maximum capacity. But most of the N95
microfiber is manufactured in Asia, and they
need masks there as much as we need them here.
So, the supply chain is stretched too thin,
meaning mask material that’s made in Asia is
staying in Asia right now.
Fortunately, ExxonMobil understands materials
science, manufacturing and supply chains, so
we’re working to use that expertise and our
connections in these areas to help. That means
looking at similar designs and materials and
talking to academics and manufacturers who can
divert their resources and retool their
machinery quickly.
“In
terms of materials for the masks, we have two
new sources. One is from a company that makes
the dust-repelling fabric for speakers for sound
systems. That material, when charged, gets to a
similar level of protection as an N95 mask and,
if used properly, can protect a health care
worker for an entire shift. A team at North
Carolina State University, which is the premier
fabric institute for polymers, has a production
line operating 10 hours per day. We’re helping
to get them going 24/7.
Of course, there’s only so much filtering
material that can be produced. So, we need to
use every centimeter of fabric effectively,
which means rethinking the mask itself.
So instead of the traditional N95 disposable
mask, we’re working on a composite rubber
facemask with small, replaceable filter
cartridges. This mask looks like the ones
painters wear. The filter fabric in the
cartridges will have the electrostatic charge,
and at the end of a shift, the doctor or nurse
can simply remove the mask, clean it and replace
the cartridges with new ones, enabling them to
use the same mask again the next day.
Would the masks’
replaceable filter cartridges contain similar
material to that of an N95 mask?
Essentially, yes. The main advantage is that we
will use far less filter material than we would
with a disposable mask, so no filter material
goes to waste.
Best of all, we’re not putting health care
workers in a position where they feel they have
to wash or heat sterilize an N95 mask, which
just reduces the effectiveness of the masks
they’ve been forced to reuse up to this point.
So how do we get from concept to rapid
production, given the current supply chain
constraints?
We used 3D printing for prototypes and
molds. After working with the medical community
and the team at the Global
Center for Medical Innovation in
Atlanta to make sure the mask is up to
standards, our medical-grade plastics experts
started working with private and government
manufacturers to create an injection mold.
Once the mold is built in the shape of the mask,
thousands of them can be produced per hour.
We’re collaborating with NASA, the Georgia
Tech Research Institute,
GE, Delta Airlines, the National Organization
for Technology Exploration and Delivery, Boeing
and the U.S.
Army Futures Command to
decide which materials can be scaled up.
ExxonMobil is Increasing Isopropyl Alcohol
Production and Also Producing Medical Grade
Sanitizer
ExxonMobil has reconfigured manufacturing
operations in Louisiana to produce medical-grade
hand sanitizer for donation to COVID-19 response
efforts in Louisiana, New Jersey, New Mexico,
New York, Pennsylvania and Texas.
Initial production of 160,000 gallons of medical
grade sanitizer – enough to fill nearly 5
million 4-ounce bottles – is being distributed
to medical providers and first responders.
Additional donation locations are planned.
“The ingenuity and dedication of our employees
to develop a consumer-ready product in record
time demonstrates ExxonMobil’s commitment to
help those in need during the global pandemic,”
said Darren Woods, chairman and chief executive
officer of Exxon Mobil Corporation. “We’re
focused on keeping our people and communities
safe while supporting frontline responders and
meeting customer needs.”
ExxonMobil has increased monthly production of
isopropyl alcohol -- a key ingredient in
sanitizer – by about 3,000 tonnes at its
chemical manufacturing facility in Baton Rouge,
Louisiana. To produce, package and distribute
hand sanitizer, the company purchased additional
ingredients and modified equipment in Baton
Rouge and at a lubricants plant in nearby Port
Allen, Louisiana.
“To stand up an entirely new process and supply
chain in a matter of weeks, while maintaining
ExxonMobil’s high standards for safety and
quality and in compliance with FDA requirements
is truly remarkable,” said Karen McKee,
president of ExxonMobil Chemical Company.
Earlier this month, ExxonMobil announced the
increased production of isopropyl alcohol, which
is enough to enable monthly production of up to
50 million 4-ounce bottles of sanitizer. The
company also increased its capability to
manufacture specialized polypropylene, used in
medical masks and gowns, by about 1,000 tonnes
per month, which is enough to enable production
of up to 200 million medical masks or 20 million
gowns.
Porvair Filtration Group’s Segensworth Division
to Supply Fully Assembled Face Shields to the
British National Health Service
As part of project “The Big Print”, Porvair has
been manufacturing face shield components using
a 3D printer, which is normally used to produce
tooling and prototypes destined for the
Aerospace, Defense and Nuclear industries.
These face shields will be donated to help
protect front-line medical staff in the NHS.
3D printers create physical objects by extruding
thin layers of plastic or other materials to
slowly build up components based on a computer
generated model. Whilst slow to manufacture, the
process allows production of components without
the associated cost and time for complex
tooling.
The company’s UK Head Office is targeting an
initial supply of 50 face shields to the project
and is currently able to manufacture 36 sets per
week. Further work is being done to improve
production rates. Each set of 3D printed
components takes approximately 1 hour 20 minutes
to manufacture, however, as with many British
manufacturers, all hands have turned to support
in the fight against the Coronavirus.
Some of Porvairs key suppliers have offered
their support in donating additional face shield
components (screens and elastic). This will
enable Porvair to provide fully assembled face
shields to local health workers.
Louis Moult, Manufacturing Engineering Manager
stated “With support from our senior management
and procurement team, we have been able to
source critical 3D printer parts from Germany
overnight which has
allowed us to
start manufacture of the face shield component.

|