WELCOME
Weekly selected highlights in flow
control, treatment and combustion from the many McIlvaine publications.
·
Briefs
·
FGD Market Offers Billions of Dollars of Profits
·
Determining the Market for Your Product at Every
Food Plant
·
Electrostatic Precipitator Upgrades
Briefs
The
FGD pump market worldwide including repairs and replacements will continue
to exceed $200 million per year and consist mostly of centrifugal
pumps. The big reciprocating pump market continues to be hydraulic
fracturing and will be expanding from the U.S. to China and Argentina.
Sinopec is the world’s largest pump purchaser but is also a supplier. Keep
up with this changing market at http://home.mcilvainecompany.com/index.php/markets/water-and-flow/n019-pumps-world-market
The
oil and gas opportunities keep shifting with tariffs, changing fuel prices,
and other variables. Does China gasify more coal or purchase more LNG? How
successful are fracking programs outside the U.S.? Where are all the
LNG projects and what is their status? All this is covered in http://home.mcilvainecompany.com/index.php/markets/energy/n049-oil-gas-shale-and-refining-markets-and-projects
There
are growing opportunities for disk centrifuges, macrofilters, valves,
pumps, cross flow membranes, cartridges and instrumentation in the fast
growing biopharm market. Will it maintain double digit growth? See some of
the answers at
The
Future of Biopharmaceuticals will Depend on Perceived Value vs Cost
Cannabis
is also a fast growing market for centrifuges and cleanrooms. We are
providing custom research in this area.
The
scrubber market is growing due to activity in sugar cane conversion to
solid fuel and ethanol, marine shipping, refining, mining, steel and
petrochemicals. Forecasts for absorbers and adsorbers are included in
http://home.mcilvainecompany.com/index.php/markets/air/n008-scrubber-adsorber-biofilter-world-markets
Activity
at chemical, steel, mining, pulp & paper and cement plants is
tracked along with profiles of each major purchaser at http://home.mcilvainecompany.com/index.php/databases/n032-industrial-plants-and-projects
FGD Market
Offers Billions of Dollars of Profits
More
than $50 billion per year will be spent on the systems, parts, consumables
and services by power companies to build and maintain flue gas
desulfurization (FGD) systems. If these systems are not meeting SO2
emission limits the power plant must cease operations. All the elements of
severe service are present: corrosion, temperature, and abrasion. As a result power companies are focused
on buying products with the lowest true cost. This translates into billions
of dollars of potential profits for suppliers.
These
profits are achievable by identifying the potential for each customer, providing
evidence of the lowest true cost and then convincing the customer
(validating the claims).
A
cost effective program is available.
FGD Most Profitable Market
Program costs less than $10,000 per year. It includes customized forecasts for each
country and each purchaser for any one of the following.
Chemicals
|
Ball Mills
|
Instrumentation
|
Compressors
|
Lime
|
Scrubbers -
Wet
|
CEMS
|
Valves
|
Pumps
|
Filters
|
Mist
Eliminators
|
Scrubbers -
Dry
|
Filter Belts
|
Nozzles
|
Stainless
Alloys
|
Fans
|
Limestone
|
Remote
Monitoring
|
Filter Bags
|
Controls
|
Pneumatic
Conveying
|
This
is an extension of http://home.mcilvainecompany.com/index.php/markets/air/n027-fgd-market-and-strategies
Identification
of each purchaser and weekly project tracking is included in http://home.mcilvainecompany.com/index.php/databases/42ei-utility-tracking-system
The
validation process with customers is accomplished through http://home.mcilvainecompany.com/index.php/silobusters/44i-coal-fired-power-plant-decisions
This
service allows the purchasers to conclude which products have the lowest
true cost. Here is a link to one of
the recent webinars https://youtu.be/1GSbwSiTZrE
The
broader Most Profitable Market Program is detailed at www.mcilvainecompany.com
Bob
McIlvaine can answer your questions at rmcilvaine@mcilvainecompany.com direct 847 784 0013 and cell 847 226
2391
Determining
the Market for Your Product at Every Food Plant
A
program to help suppliers of flow and treat products sell to food producers
has been introduced by the McIlvaine Company. It predicts the purchases of
any product based on the tons of a specific food produced for the next five
years. It provides enough technical details and process flow diagrams so
that suppliers can craft lowest total cost of ownership (true cost) white
papers. A route to the decision makers is also provided. The general program is explained at www.mcilvainecomany.com under Most Profitable Market Program.
Specific
forecasts are available for each type of air pollution control, liquid
filter or separator, pumps, valves, dryers, heat exchangers,
instrumentation, software, steam and electricity generators e.g. for
bagasse. Analyses of the potential
from each producer also takes into account byproducts or finished products
which are manufactured. For sugar this would include alcohol, ethanol and
power generation. Here are the major food segments analyzed
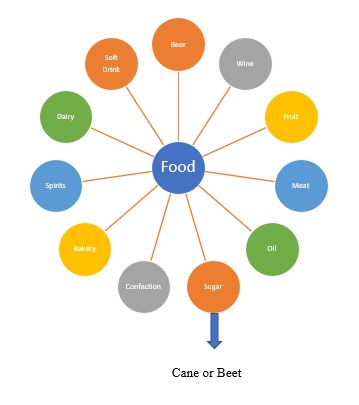
Cane
sugar is being used as an example. It involves a number of flow and treat processes.

The
quantity of crushed cane or bagasse is more than the amount of sugar
produced. The bagasse is a good fuel. Sugar mills are combusting it to
generate steam for their use and electricity for use and for sale. They are
also major producers of alcohol and ethanol. Therefore companies such as
Cosan and Tereos, who are major cane sugar producers are bigger prospects
than large beet sugar producers in Europe and the U.S.
Flow
and treat analyses and forecasts are based on the present and future
production in each country and for each significant producer. Here is an
example of production forecasts for total sugar production through
2024. We also have these for the cane
and beet sugar segments.
Sugar Production
- 1000 MT
|
|
|
2016
|
2017
|
2018
|
2019
|
2020
|
2021
|
2022
|
2023
|
2024
|
Afghanistan
|
0
|
0
|
0
|
0
|
0
|
0
|
0
|
0
|
0
|
Albania
|
4
|
5
|
0
|
0
|
0
|
0
|
0
|
0
|
0
|
Algeria
|
0
|
0
|
0
|
0
|
0
|
0
|
0
|
0
|
0
|
Angola
|
40
|
55
|
65
|
60
|
60
|
61
|
63
|
64
|
66
|
Argentina
|
2060
|
2050
|
1870
|
1665
|
1680
|
1726
|
1773
|
1821
|
1871
|
Armenia
|
3
|
3
|
0
|
0
|
0
|
0
|
0
|
0
|
0
|
|
|
|
|
|
|
|
|
|
|
|
The
data is also available for the 250 largest sugar producers. We provide
profiles and not only sugar production but also co-products such as
ethanol.
Sao
Martinho
Sao
Martinho is a well-established Brazilian company that can trace its roots
back as far as 1938. Sao Martinho was initially formed in a series of
corporate take overs in which sugar mills were purchased and incorporated
into the main corporate structure of Sao Martinho. Prior to 2006, Sao
Martinho was known as Companhia Industrial e Agrícola Ometto. Today, Sao
Martinho is one of the largest sugar companies in Brazil. Like the other
major companies, it does not solely produce sugar, but also produces sugar
ethanol as well as other sugar cane products. Sao Martinho currently has
two mills dedicated to sugar and sugar ethanol production.
These mills are known as the Iracema Mill and Sao Martinho Mill.
It expects to process 8% more
sugarcane in 2019/20 compared with the prior crop year. The company sees
its cane crush rising to 22 million tonnes thanks to “better weather
conditions and projects aimed at increased productivity, However, the
amount of sugar derived from each tonne of cane will fall slightly. Sao
Martinho said the total recoverable sugars are expected to be 139 kilograms
per tonne, a 2% decrease from the previous season.
Sao Martinho predicted it
would produce between 1.055 million to 1.4 million tonnes of sugar and 915
million to 1.1 billion liters of ethanol in the 2019/20 season.
Here are sugar
production forecasts for 2019 for some of the companies.
Company
|
Location
|
Production
1000 tons 2018
|
Market share %
|
COSAN LIMITED
|
Brazil
|
4,000 (plus ethanol)
|
2.1
|
Sudzucker
|
Germany
|
4,800
|
2.5
|
Tereos
|
France, Brazil
|
2900
|
1.5
|
Nordzucker
|
Denmark,
Germany
|
2500
|
1.3
|
Wilmar
|
Australia
|
2000
|
1.0
|
British Sugar
|
UK
|
1500
|
0.7
|
Mitr Phol
|
China
|
1300
|
0.6
|
American Sugar
|
Chalmette LA
Refinery
|
1,000
|
0.5
|
E.I.D.-PARRY (INDIA) LTD. .
|
India
|
1600
|
0.8
|
American Crystal Sugar
|
Beet in Upper
Mid-west
|
1500
|
0.7
|
Rogers Sugar Inc.
|
Vancouver Only
|
240
|
0.1
|
Nanning Sugar.
|
China
|
700
|
0.4
|
We
analyze important product developments such as manufacture of cellulosic
ethanol.
Raizen completed
construction of its first cellulosic ethanol plant where the ethanol will
be produced from sugarcane residue. The company invested R$237 million in
the plant that will produce 40 million liters of ethanol from sugarcane
residue. The plant is located in the city of Piracicaba in the state of Sao
Paulo and right next door to one of Raizen's sugar mills that makes sugar
and ethanol from sugarcane.
The sugarcane residue
from the sugar mill is currently being burned to generate electricity to
run the mill with the excess electricity sold back into the electrical
grid. The company is now going to divert some of the sugarcane residue to
its new facility to produce ethanol. The company feels there are a lot of
saving and synergies by placing both plants next door to each other.
Raizen originally
estimated that its company-wide ethanol production would increase 50% by
producing second generation ethanol. The company had planned to construct
seven more cellulose ethanol plants in Brazil by 2024. All of the
facilities would be built next door to their existing first generation
ethanol plants that use sugarcane. All of the new plants combined could
produce up to one billion liters of cellulosic ethanol. However, technical
and economic factors have slowed that development. These problems have now
been resolved and the company expects cellulosic ethanol to be an important
revenue source.
We
search for data which will help determine the true cost of a product such
as a filter belt or drum filter.
Cordoba
belt filters at the Raizen Costa Pinto plant are shown in the YouTube video
https://www.youtube.com/watch?v=EZtc_QaR0lw
The
following paper is an example of gathering all the evidence. In an effort
to compare belt filters with rotary drum filters several areas of interest
were investigated over the 2012 and 2013 crops. These included pol losses,
bagacillo ratio (bagacillo % feed/mud solids % feed), filter retention (mud
in filter cake/mud in feed), filter capacity (filter cake production and
removal of mud), belt wash water loss and flocculant usage.
The
pol % filter cake average of 3.47. Pol % filter cake from drum filters
ranged from 1.00 to 7.36 and averaged 4.08% pol. Belt filters had an
average pol % filter cake of 2.36 with a range of 0.46 to 5.86%.
Crop
flocculant usage averaged 0.022 lbs./ton cane. Belt filters used a little
more flocculant (0.024) on average than drum filters (0.020). On average
5.21 lbs. pol/ton of cane are lost in filter cake for rotary drum filters.
Belt filters lost on average 2.71 lbs. pol/ton cane. This included losses in
the belt wash water based on a rate of 100 gallons per minute. The overall
average filter cake production was 1443 lbs./hr./ft. width. Drum filters
averaged 1080 lbs. filter cake and ranged from 128 to 2606 lbs. filter
cake/hr./ft. width. Belt filters averaged 2781 lbs./hr./ft. width, almost
three times the amount for drums, and ranged from 1509 to 4027 lbs./hr./ft.
width.
Regarding
belt filters only, the capacity seems to be very high with sugar losses
comparable to that of drums. Maintenance costs have yet to be determined.
Options for disposal of belt wash water should be considered. https://www.lsuagcenter.com/MCMS/RelatedFiles/%7BBB9E504C-EEAD-4D0C-8249-C67F42F775AA%7D/2014.pdf
A
sales program can be constructed with the detailed knowledge of the future
purchases at each plant. the best
contacts are easily determined through a LinkedIn initiative. Raizen has over 11,400 contacts. But if you want to talk about belt
filters at the Costa Pinto plant you can start with the 18 people involved
in filtration or the 185 people at the Costa Pinto plant.
Raizen LinkedIn Contacts
|
Subject
|
# of people
|
Total on
LinkedIn
|
11,400
|
Centrifuge
|
2
|
Filtration
|
18
|
Pumps
|
69
|
Environment
|
1000
|
Pollution
|
13
|
Costa Pinto
|
185
|
Engineering
|
3748
|
Vice President
|
189
|
Cellulosic
Ethanol
|
22
|
For
more information on the flow and treat program for the food industry
contact Bob McIlvaine at rmcilvaine@mcilvainecompany.com or 847 784 0013 or cell 847 226 2391.
Electrostatic
Precipitator Upgrades
Discussions
about precipitator power supplies at PowerGen will take place at various
stands as well as in pre-arranged and impromptu discussions on the exhibit
floor and conference area. Paul Leanza and Dan Holt of KraftPowercon have
volunteered to help maximize the discussion value and activity. A recorded
interview with them can be the foundation of some of the discussions.
Sessions: None of the sessions will directly
address the precipitator upgrade question but Babcock Power has one speech
which is tangentially relevant.
Exhibitors: CECO
- AVC supplies precipitator controls. Doosan
provides precipitator control systems. Hamon
provides precipitators and control systems. R&R Beth provides precipitators and control systems.
Southern Environmental
provides precipitators and control systems.
Wood acquired Wheelabrator which supplies
precipitators and controls.
We will
continually be creating the following
directory of attendees, exhibitors and speakers who are interested
in discussing precipitator upgrades.
KraftPowercon presented their
line of precipitator control, power, and safety products in a recorded
interview. It is accessed at https://youtu.be/d_pVvdIYJHc. The
slides accompanying the presentation are shown at
http://www.mcilvainecompany.com/Decision_Tree/subscriber/Tree/DescriptionTextLinks/HV_productsolutions_Sept_2019.pdf
Paul Leanza and Dan Holt discussed their product
capabilities and how they have seen them applied effectively. The
discussion of each new item and its technical merits continues to circle
back to how to apply each effectively at best cost. This 52 minute
interview provides good coverage of the options of supplies and controls
which are available. It can be addressed by other suppliers as a reference
point for hearing all sides of the issues.
Dan is a former pulp mill engineer. Paul owned a
precipitator consulting company, which merged with KraftPowercon. Both
demonstrated the process knowledge, which allows the company to provide
solutions and not just products.
KraftPowercon offers all variations of power
supply. Dan and Paul explained that
single phase TR sets are reliable and modest in cost. But they do not
deliver the high efficiency needed in many applications.
Single-phase
TR unit
• 120 Hz current ripple
• Results in ˜ 35-45 %
ripple voltage on an ESP load
• Voltage peaks limits the
current into the ESP
The 3 phase TR set is more efficient but also more costly
3-phase TR unit
• 360 Hz current ripple
• Results in ˜ 0.5-1.5 %
ripple voltage on an ESP load
• 30–40% higher current into the ESP
compared to single-phase TR
Switch Mode Power supplies are efficient with low installation cost.
Maintenance has been an issue with this technology being applied to ESPs.
High frequency SMPS
• 24kHz current ripple
• Results in < 1 % ripple voltage on an
ESP load
• 30–40 % higher current
into the ESP compared to single-phase TR
To rectify the problems with SMPS KraftPowercon
introduced a version with features to make it more reliable.
SmartKraft
DC
|
Competitor
|
Oil Cooled
|
Air Cooled
|
12 IGBTs
|
4-6 IGBTs
|
Aluminum Tank
|
Steel Tank
|
Amplitude Control
|
Frequency Control
|
KraftPowercon
also points to improvements in controls.
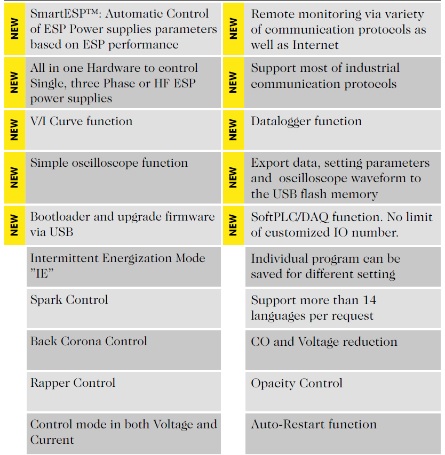
NWL
NWL
is a major supplier of power supplies around the world. NWL states that its
unique integrated design, places the power supply and control system on a
common assembly. The NWL PowerPlus™ has been installed on precipitators in
many different industries and applications throughout the world. This
product is claimed to provide the
following benefits to its users:
- Increased
collection efficiency
- Decreased
kVA for the same amount of power applied to the field
- Faster
spark response with less wasted spark current
- Higher
Reliability
- Significantly
higher power factor when compared to a conventional TR
- Lower
initial installation cost
- Reduced
space requirement with integrated design
- Able
to facilitate buss and guard or cable for HV connection
B&W
B&W has supplied thousands of precipitators. The most common way
to improve the performance of an ESP, wherever it is located says B&W
is to boost its corona power. The relationship between specific corona
power (watts/1,000 acfm of gas flow) and collection efficiency is well
understood and is a common upgrade. Other ESP efficiency improvements are
possible, such as reconfiguring compartment geometry, increasing plate
area, or adding additional fields, although each upgrade usually requires
replacing or upgrading existing power supplies. The best option is to
select a power supply that can efficiently boost corona power output and
maintain high operating reliability.
The single-phase power supply design has limited upgrade potential
to meet MATS, so Babcock & Wilcox (B&W) began the process of
identifying better power supply options.
The increase
in corona power from a low ripple power supply can be achieved with several
different technologies (HFPS, TPPS, MFPS).
Integrating
all components into one package (HFPS) has the advantage of the most
compact configuration. This can have the disadvantage of placing the
control section for the power supply in a harsh environment which affects
service life and maintenance.
Providing a
separate transformer and control cabinet (MFPS, TPPS) has the advantage of
placing the electronic controls in a controlled environment and allows for
duplicate sources of supply. This has the disadvantage of the need for a remote
control cabinet and larger size and weight.
MFPS and TPPS
use passive cooling while HFPS designs require active cooling. The increase
in components and complexity for active cooling increase cost and
maintenance. HFPS designs provide low ripple at higher cost, lower
reliability, but in a smaller, lighter integrated package. MFPS and TPPS provide low ripple at lower
average cost, higher reliability, but in a larger, heavier package with a
separate control cabinet.
The HFPS,
MFPS, and TPPS provide the lowest ripple voltage on an ESP load. A field
test showed the TPPS produced an average 50% higher power in the ESP
compared to the single-phase precipitator power supply. This suggests that
like other low ripple power supplies, the TPPS can produce higher ESP
collection efficiencies. More than 900 installations of TPPS have
demonstrated reliability. The availability of all sections of an ESP allows
plant owners to achieve maximum PM reduction
Capital cost is also a significant consideration in the selection
process of ESP power supplies, and the differences are significant. For
example, if the single-phase power supply cost is 1.0, then the relative
cost for a like-sized high-frequency SMPS ranges from 1.49 to 2.31. A
like-size low-frequency three-phase power supply’s relative cost is only
1.12 to 1.17.
The predicted reliability of a power supply is difficult to
quantify. The reliability track record of the single-phase ESP power supply
is excellent, and many installations have been in service for over 40 years.
This is a reliability benchmark that low-ripple power supply designs must
match. Anecdotal evidence finds that high-frequency power supplies have
experienced a poor reliability record; although it has improved in recent
years, it remains lower than for single-phase designs.
Field test results at Duke Power
confirmed that the three-phase power supply typically produced 50%
more corona power delivered to the ESP than from a conventional power
supply (average three-phase power/average single-phase power) with low
total harmonic distortion. The installation costs were on par with a
standard single-phase power supply. There were no failures of the
three-phase power supply during the six-month test run.
https://www.powermag.com/choosing-an-esp-power-supply-for-improved-particulate-control/?pagenum=4
and https://www.babcock.com/-/media/documents/resources/gated-content/br-1941.ashx?la=en&hash=ABB2C7B1FFAF56483BB8CDF68D2E29CEF3DD6A07
CECO
CECO is an exhibitor and will be displaying systems,
dampers and precipitator controls. AVC Specialists brand Powercon™ 900 Automatic Voltage
Controller is the latest of its precipitator Automatic
Voltage Controller systems. It is designed to be a simple upgrade
for older models, as well as a
replacement for most older competitor’s models.
With color touch screen display, and easy-to-use
operator HMI, all functions can be controlled, edited, and troubleshot,
without ever having to open the door, which can be a time consuming problem
at most facilities. the operator interface offers easy access to status,
parameter settings, fault history, and tuning screen, including a built-in
oscilloscope.
Hamon
Hamon
is an exhibitor and arguably the
world’s first supplier (Research Cottrell Precip for a cement plant 100
years ago) HR-C works with selected
suppliers to provide advanced microprocessor controls and the latest in
transformer/rectifiers and switch mode power supplies to maximize
performance. So they can offer third
party analysis of the options.
Doosan
Doosan is an exhibitor. Doosan Lentjes can rely on the
experience accumulated in one of the largest precipitator databases
throughout the world due to the fact that over 6,000 electrostatic
precipitators (ESP) have been built to date.
R&R Beth
The company is an exhibitor and has supplied
precipitators for many different industries in many locations of the
world. It uses high voltage power
supplies and its views on the options will be sought.
Southern Environmental
It is an exhibitor and part of the SEI-Group comprised of three
operating units: Southern Environmental, Inc. Southern Erectors, Inc.
and Thermal Systems Group. Internationally, SEI-Group has performed
projects in Antarctica, Argentina, Bolivia, Brazil, Canada, China, India,
Mexico, Qatar, Russia, Singapore, South Korea, Sweden, Taiwan and
Thailand. SEI started as a
specialist in maintenance and repair of precipitators but started designing
and building new precipitators some years ago. Its perspective on controls
will be a valued addition.
Wood
Wood acquired Wheelabrator from Foster Wheeler. It is an
exhibitor and also exhibited at POWERGEN Asia in September
in Kuala Lumpur, Malaysia. It has been supplying air pollution control
equipment for more than 50 years. Precipitator projects have ranged up to 5 million
cfm. Its views on power plant
supplies will be welcomed due to its extensive experience.
Click here
to un-subscribe from this mailing list
|